Follow us on LinkedIn
Companies use various costing methods to establish the unit cost of manufacturing a product. Determining these costs is highly crucial in understanding how a company’s production process works. On top of that, it provides a base for measuring the price to charge for the underlying product. One of the methods that can help in this regard is absorption costing.
What is Absorption Costing?
Absorption costing is a costing method that companies use to determine the cost of a product. This method falls under managerial accounting, which includes establishing those costs. However, absorption costing doesn’t only apply to managerial accounting. It is also crucial in establishing costs under financial accounting under different accounting standards.
Absorption costing involves absorbing a company’s variable and fixed manufacturing overheads into a product’s cost. This approach differs from other methods that only consider variable material and labour costs. Another name for absorption costing is full costing since it includes all the costs associated with manufacturing a product.
Overall, the absorption costing method involves accumulating all costs associated with a production process. Later, it apportions those costs to individual products. These costs then help establish the value of inventory that companies keep. Furthermore, it also allows companies to estimate the cost of goods sold during an accounting period.
What are the components of Absorption Costing?
Absorption costing considers various components when establishing a product’s cost. Some of these include the following.
Direct material
Direct material includes any raw materials that contribute directly to a product. However, it does not involve any items that do not form a part of the finished product. For example, for companies that manufacture furniture, direct material will consist of wood.
Direct labour
Direct labour includes any costs paid to workers in exchange for working on a product. These costs must contribute directly to the finished goods. For example, salaries and wages paid to production line workers form direct labour costs.
Variable manufacturing overheads
Apart from direct labour and direct material, companies may also incur other variable manufacturing overheads. These overheads include expenses necessary to operate a production facility and relate to production volume. Like direct material and labour, these costs also vary with volume.
Fixed manufacturing overheads
Apart from variable manufacturing overheads, absorption costing also considers fixed overheads. These are similar to the above as it includes expenses to run a manufacturing facility. However, these costs do not change with production levels.
What are the advantages and disadvantages of Absorption Costing?
Absorption costing can provide several advantages. One of the most prominent of these includes being compliant with most accounting standards. Similarly, absorption costing considers all production-related costs when evaluating inventory. This way, it allows companies to value their stock more accurately. Absorption costing can also provide better results for smaller companies and dynamic environments.
However, absorption costing can have some disadvantages. Some companies may prefer other methods such as marginal costing since it helps in better decision-making. Similarly, absorption costing can also impact the accurate presentation of profits. Some companies may use this method to manipulate profits and overstate inventory.
Conclusion
Absorption costing is a product costing technique that considers all production-related costs. This method can help in evaluating inventory and establishing the cost of goods sold. Similarly, it is also compatible with accounting standards. Absorption costing requires four components to calculate product costs. This method can have several advantages and disadvantages, as mentioned above.
Further questions
What's your question? Ask it in the discussion forum
Have an answer to the questions below? Post it here or in the forum
Meta rolled back January 6-era restrictions on former President Donald Trump's social media accounts ahead of the Republican National Convention.
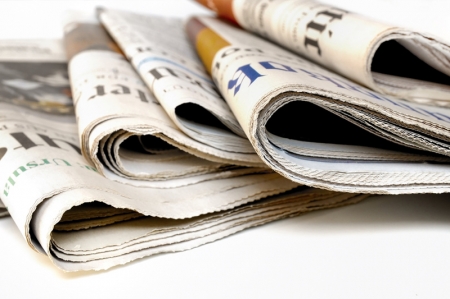
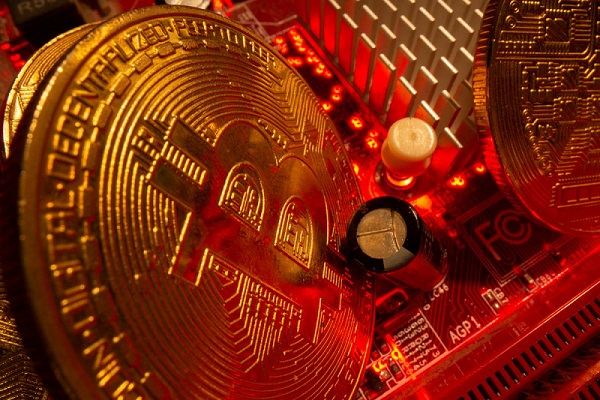

June saw 75 filings, up from 62 in May and above the pandemic-era peak of 74 in July 2020, according to S&P Global Market Intelligence.
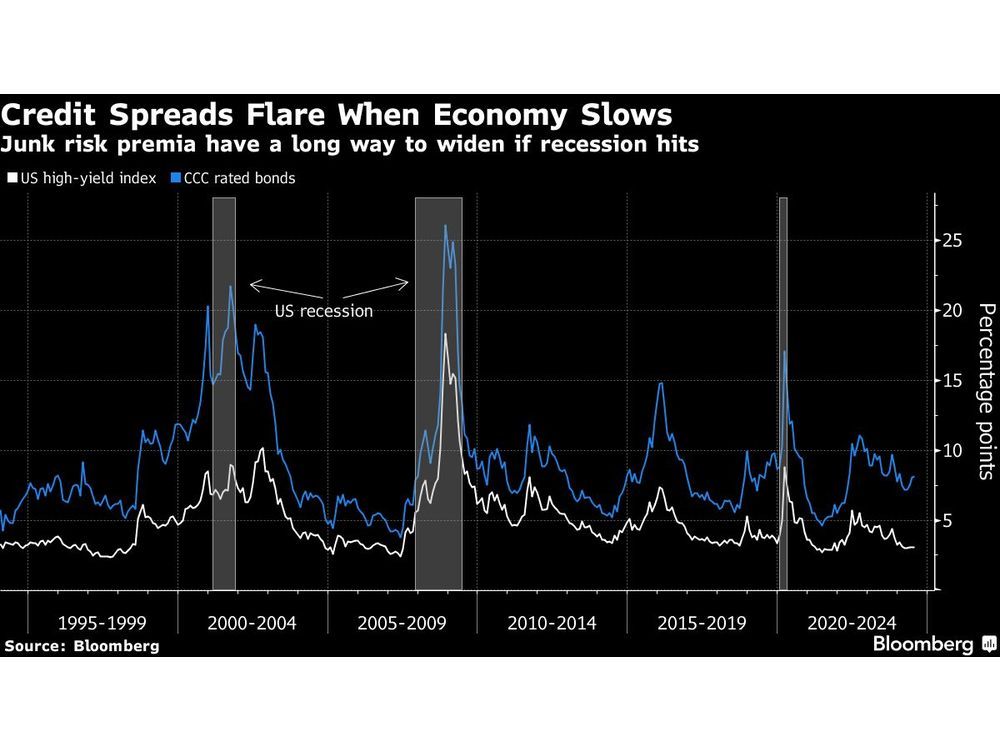
Credit markets are breathing a sigh of relief after inflation data showed price pressures are cooling broadly, but a weakening economy poses fresh risks to corporate debt.